Research and development
In most company structures, the process of the whole product development track is segmented and assigned to several teams and departments. All our industrial designers have made it their professional focus to master and amalgamate all these fields of expertise and activities in themselves as one-man/woman R&D units.



Research and development
In most company structures, the process of the whole product development track is segmented and assigned to several teams and departments. All our industrial designers have made it their professional focus to master and amalgamate all these fields of expertise and activities in themselves as one-man/woman R&D units.
This consolidated under one hat approach allows more design freedom because the designer is simultaneously fully aware of all the engineering and technological restrictions. At the same time, he/she has full control and knowledge of the selection of production materials and the production facilities. The reduced necessity for inter-team communication in this model shortens the overall timeline of the product development process.
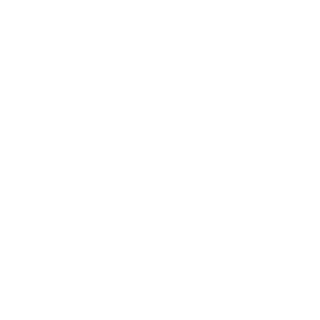
research
Here we empathize, define and ideate. Our first goal is to research and gain an empathic understanding of the problem you are trying to solve. We learn more about your industry and we investigate your competition (direct and indirect) and similar or related products that exist on the market. Then we analyze our observations and synthesize them in order to define the core problems that we have identified up to this point. Then we start to "think outside the box" to identify new solutions to the problem statement we have created, and we can start to look for alternative ways of viewing the problem.
engineering
After we have defined the problems and features and have created “outside the box" ideas to solve them, we start the virtual development of the product. Our designers will create several 3D conceptual design solutions. In a joint interactive effort, your and our teams will select the best design concept and revisit it in several iterations if necessary until we are all satisfied that we are on the right track. We have finalized the virtual design solution at the point when we are all convinced that the problem set has been solved and the visual and mechanical design of the product is ahead of the competition. Then we can move to physical prototyping.
prototyping
Using different technologies (3D printing, CNC milling, etc.), our design team will produce a number of inexpensive versions of the product, scaled down if necessary, so they can investigate the problem solutions generated in the previous stage. This is an experimental phase, and the aim is to further identify the best possible solution for each of the problems identified during the first stages. The solutions are implemented within the prototypes, and, one by one, they are investigated and either accepted, improved and re-examined, or rejected on the basis of the users’ experiences. By the end of this stage, the design team will have a better idea of the constraints inherent to the product and the problems that are present, and have a clearer view of how real users would behave, think, and feel when interacting with the end product.
verify
Prototypes may be shared and tested within the team itself, in other departments, or on a small group of people outside the design team. Together with your team our designers will rigorously test the complete product using the best solutions identified during the prototyping phase. This is the final stage of R&D, but in an iterative process, the results generated during the testing phase are often used to redefine one or more problems and inform the understanding of the users, the conditions of use, how people think, behave, and feel, and to empathise. Even during this phase, alterations and refinements are made in order to rule out problem solutions and derive as deep an understanding of the product and its users as possible.